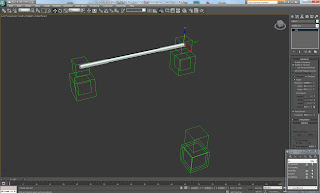
using the percentage on path attribute i used a float expression to modify the position of the suspension anchor when the wheel is moved. the move its moved the more the effect.
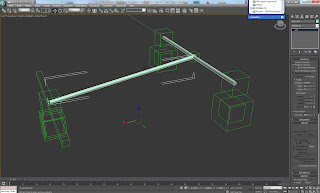
i then linked the two axles down the middle of the truck so the body can be effected when the supsension moves.
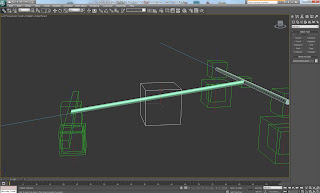
another dummy is then created to link the truck body.
orientation constraints are used to affect the box.
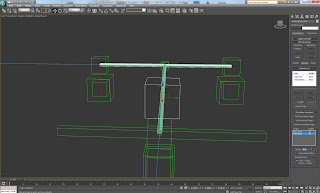
as the truck only has 1 front wheel i created another dummy and streched it to symbolise a front axel even though it is a static box.
i think i missed this out last time which cause the problems.
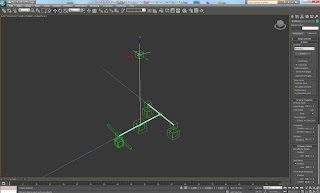
an ik solver is used to average the body momentum movements to help it look more realistic.
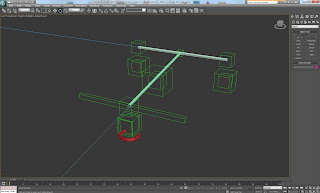
i then created a spline arc and increased the thickness to create a handle to control the drift. all the other componants were then linked to it.
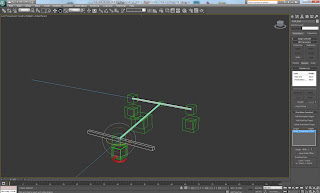
due to the centre axel not being horizontal i had to rotate the pixot point to correctly align it to the front wheel.
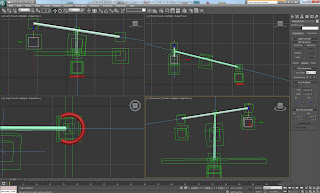
the suspention works nicely affecting the body pitch and roll when the wheels are moved.
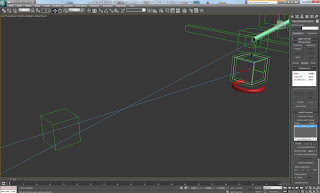
i then create a dummy and aligned it with the steering hub dummy, this is the controller to steer the front wheel.
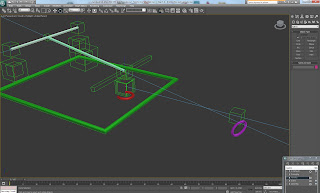
I then created a root, steering and momentum handle to control the movement of the rig
the root is the main handle that all the others link too.
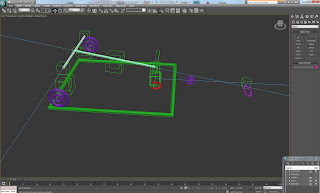
i then copied the wheel travel line and linked a donut spline to it. these are then wire parametered to the wheel hubs to allow me to select and move the wheels height more easily.
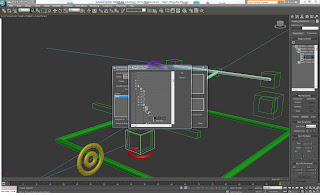
on the root spline addad a variable holder modifier and created some variables to put into there.
these are then used to controll the wheel rotation speed.
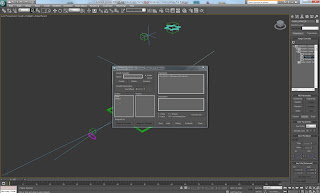
this scary looking window links the variables by a mathmatical calculation to rotate the wheel.
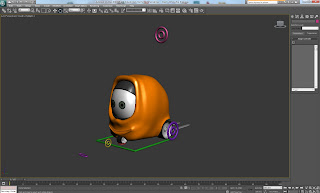
rig complte. now for the testing of the mesh.
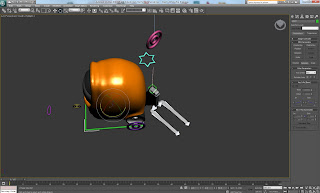
as the vasy majority of the rig is linking some times you get undesired behavior. when rotating the root the forks werent following the rotation
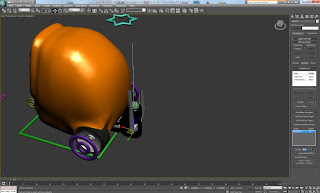
as you can see rotating the root 180 the forks are actually underneath the mesh which is not the desired effect.
this is fixed with a simple orientation constraint,
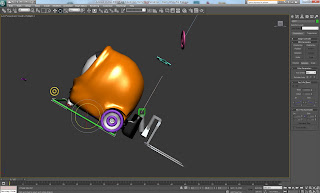
when rotated the bones of the forks were misbehaving and the handle for the lift was rotateting (this is more of an aesthetic problem)
again this was fixed with a simple orientation constriant.
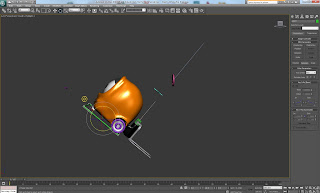
bones fixed!
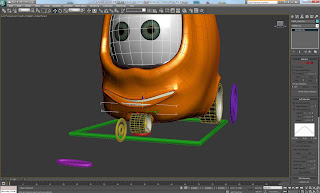
i added some teeth to the mesh as the mouth seemed a bit wide and empty
No comments:
Post a Comment